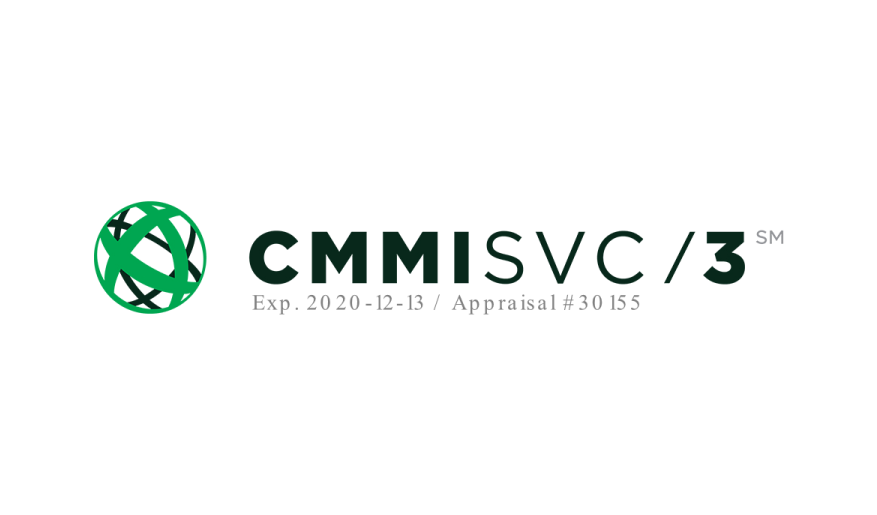
The work at Vision Technologies is driven by the six guiding principles of its corporate culture. Taken together, these principles allow the company to achieve its goal of “delivering world-class customer service and quality.”
What does “world-class quality” look like? How do we get there? And, once we achieve it, how do we maintain it? Do we bolt it on or do we build it in? The answer is, “Yes.”
Quality Control (QC)
It is important that we inspect work to ensure that it conforms to each customer’s requirements. In so doing, we inspect in quality. When done properly, QC allows us to find deficiencies and correct them in a timely manner. However, by its very nature, QC does not prevent inferior quality because it does not measure or evaluate the process whereby work is accomplished. It only evaluates outcomes. By its very nature, it is externally imposed, product focused, and reactive.
Quality Assurance (QA)
On the other hand, the goal of QA is to prevent non-conforming work in the first place. As opposed to QC, it is internally established, process-focused, and proactive. For quality assurance to be effective it must pervade the entire organization – everyone is responsible for the quality of products and services.
Total Quality Management
Vision has embedded In-Process Quality Control (IPQC) in its operations, to provide comprehensive and lifecycle, quality control to ensure seamless execution. Teammates have 100% performance visibility, and the tool allows Vision project managers to properly stay abreast of, and manage, multiple simultaneous projects.
Layered on top of that are Operational Guidelines – the process manual for building quality in to day-to-day operations. These guidelines:
- Set expectations for the behavior expected from team members;
- Create a discipline for operating as expected;
- Provide each team member an overall view of the company’s day-to-day operations;
- Detail roles and responsibilities of each team member to convey ownership and teamwork;
- Encourage accountability for every individual; and
- Enhance team member judgment to allow for decision-making at all organizational levels.
Taken together, Vision’s QC and QA comprise a total quality management system. Both elements provide value and address distinct aspects of providing world-class quality. The following example shows the positive effect of this double-barreled approach.
Case Study
Vision was awarded an IT support contract for a large government agency. It soon became apparent that the quality of various aspects of the program was substandard. A prime example was the fidelity of the asset inventory database.
First, Vision “bolted on” quality. Business rules were written for each data element to delineate acceptable and unacceptable values. At the same time, a statistically significant random sample of the database was generated and audited. By the end of the first year, accuracy had risen by eleven percentage points. The following year saw another nine percent gain – well in to the Excellent range for this Service Level Objective (SLO). Audits were subsequently reduced in frequency from quarterly to semiannually. Other QC-related activities included a weekly validation of the database against the business rules to find input errors and comparing the database to Microsoft System Center Configuration Manager (SCCM) reports.
To accelerate and sustain the quality of the database, Vision undertook various process-oriented initiatives. First, the business rules written as part of the initial QC effort were memorialized in a data dictionary and then engineered into a template that technicians could use when submitting changes to the asset inventory. All the interdependencies between elements were captured so that inputs that violated business rules were highlighted and could be corrected before submittal. Standard Operating Procedures (SOPs) were reviewed and, where appropriate, process steps were added where the SOP and the asset inventory intersected. As a result, the audited accuracy of the asset inventory has remained above 95 percent for the last four years.
Further Steps
The Professional Services Business Unit, of which I am a part, has taken our emphasis on quality to the next level. The Unit underwent an appraisal by the CMMI Institute to determine our maturity level for delivering services. The Institute appraised our maturity at Level 3, meaning that we use defined processes for managing the work we perform. We determined that we are doing a lot of things right; but, there is always room for improvement – which we have undertaken. By incorporating QC and QA into our CMMI-SVC processes, we ensure that we can meet the goal of delivering world-class customer service and quality.
Contact us to experience world-class customer service and quality.